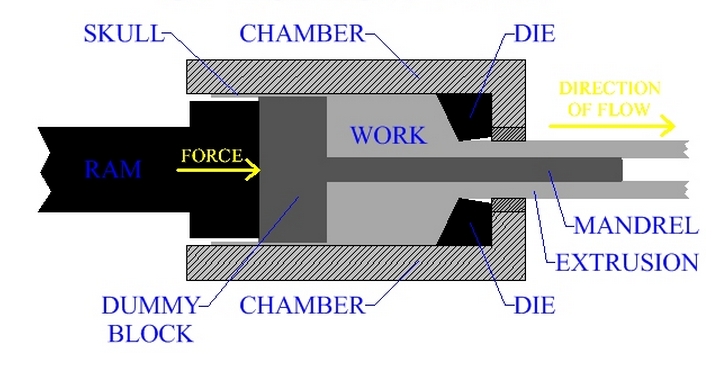
Direct or Forward Extrusion
As discussed in previous Blog on Extrusion Process, extrusion process are mainly of three types- Direct or Forward Extrusion, Indirect or Backward Extrusion & Hydrostatic Extrusion. This blog would speak on Forward or Direct Extrusion.
Direct Extrusion, also known as forward extrusion or in-line compounding, is used greatly in production of semi-finished products including films, plates, profiles and even tubes in one process step. The intermediate steps of pelletizing are not needed in forward extrusion, thereby being very economical. It requires very little investment and has considerably low operating costs and energy requirements for extrusion. Till date, certain products can only be manufactured by in-line compounding owing to the single-stage direct extrusion needed. In direct extrusion, final product quality is the most important decisive factor in the complex production process.
Direct Extrusion is the most common extrusion process carried out globally. The equipment consists of a cylinder or container which is loaded with a heated billet. On the other end, the ram or plunger compresses the metal billet against the container walls and die plate, causing metal flow in forward direction across die opening.
Direct extrusion when carried in hot conditions leads to formation of oxide scales on outer surfaces of work piece causing a negative influence on the operation. Accordingly, it has become a mandatory practice to place a dummy block ahead of the ram. This dummy block is basically a solid disc having slightly larger diameter than the chamber and billet. As the process proceeds, the outermost surface of the billet is not extruded, remaining in chamber. This material also called as skull, is a thin shell, which is removed later before the process restarts. This skull, greatly comprises of the formed oxide scales of the billet.
Hollow or even semi-hollow extruded products can be achieved by direct extrusion. This is attained by using a mandrel attached to the dummy block. A hole is created through the billet, parallel to the movement of the force applied by the ram. The mandrel is fitted within this hole. As the operation begins, ram is forced forward and the extruded material flows between mandrel and die surface forming the hole-part. The interior portion of the hollow part is thus formed by the mandrel whereas the outer portion is done by the extrusion die.
In direct extrusion, owing to relative motion between heated metal billet and cylinder walls, the frictional forces are very high. Accordingly, frictional lubricants are used in higher quantities to fasten the process. The cylinder is cooled after every extrusion to reduce any damage to it.
The major drawback of direct extrusion is the high amount of force needed to extrude the billet. This force is very high as compared to indirect extrusion because of higher frictional forces developed by the movement of the billet across the entire length of container. The amount of force is very high at the beginning of process and slowly recedes as the billet is used up. However, again at the end of billet, the force has to be increased greatly as the billet is thin and the material must flow radialy to exit the die.
Bharat Industries with its 40 years of experience in Extrusion Process along with its extensive process understanding and system competence of our specialists, can provide you high-quality extrusion dies to achieve utmost results in direct extrusion.
This entry was posted on Thursday, December 5th, 2013 at 1:23 pm and is belong to category Blog.